TRU Education Series - What is Cold Chain Logistics & Who Makes the TRU
- Michael Coggins
- May 20, 2024
- 6 min read
Updated: Mar 14
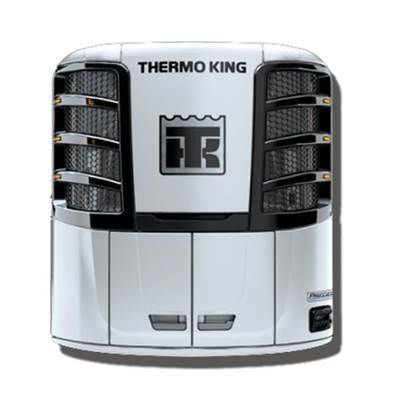
Transport Refrigeration Units - TRU
Transport Refrigeration involves the equipment - the TRU - used in the supply chain to move temperature-sensitive cargo from one place to another. There are many types of of transport refrigeration equipment in use, from massive container ships with refrigerated boxes that move fresh produce across an ocean, to small rooftop climate-controlled vans that deliver flowers in time for Mother's Day. In the past 50 years, transport refrigeration has become an integral part of the food and medical supply chain. This is largely due to advancements in TRU technology.
So what is a TRU anyway? The TRU or Transport Refrigeration Unit, is a piece of mechanical equipment designed to use the science of heat transfer to maintain the temperature integrity of perishable products. So who makes the TRU?
Meet TRU Makers:
The two largest makers of transport refrigerated equipment are Carrier Transicold and Thermo King. Their product lines include a variety of refrigerated equipment. For our purposes, we're going to focus on the specific TRU technology that's used in over-the-road supply chain operations. This is the equipment that we support here at Salem.
(Note: TRU or Transport Refrigeration is commonly referred to as the "reefer;" nothing wrong with this, but we will use the appropriate term for the equipment as found in factory publications which is TRU to avoid negative associations that often accompany the term "reefer" i.e. marijuana or cannabis use.)
There are two groups within the category of over-the-road TRUs. The first group of TRUs are the self-powered units. These will include truck and trailer units. SPUs deploy a variety of innovative technologies including diesel and electric motors to control climate control operations while functioning independently of the host vehicle. The second group of TRUs are the direct drive units. These are mostly found on trucks and vans. DDUs are used in smaller delivery applications and rely on the engine of the vehicle to turn an automotive-style compressor for climate control operations. Direct-drive units differ in several ways from self-powered units and at times may require a little different approach to service and maintenance. Let's take a closer look at these differences.
Self-Powered
Self-powered units operate independently of the truck or trailer, hence the name self-powered. They usually feature a diesel engine and/or other alternative electrical power sources, like standby motors, that can perform climate control operations. Self-powered units are large-capacity units, with powerful cooling systems. They're capable of keeping deep frozen loads safe even in some of the harshest climates in the world. Self-powered TRUs are used mostly for transporting temperature-sensitive products across the supply chain, but they can be used in stationary onsite cold storage applications. Often breweries, hospitals, grocery stores, florists, and food suppliers outgrow their current cold storage space or just need additional space during busier holiday seasons like Thanksgiving and Christmas. In such cases, SPUs can be set up to operate as stand-alone storage units providing a safe and cost-effective alternative for solving these kinds of climate control dilemmas.
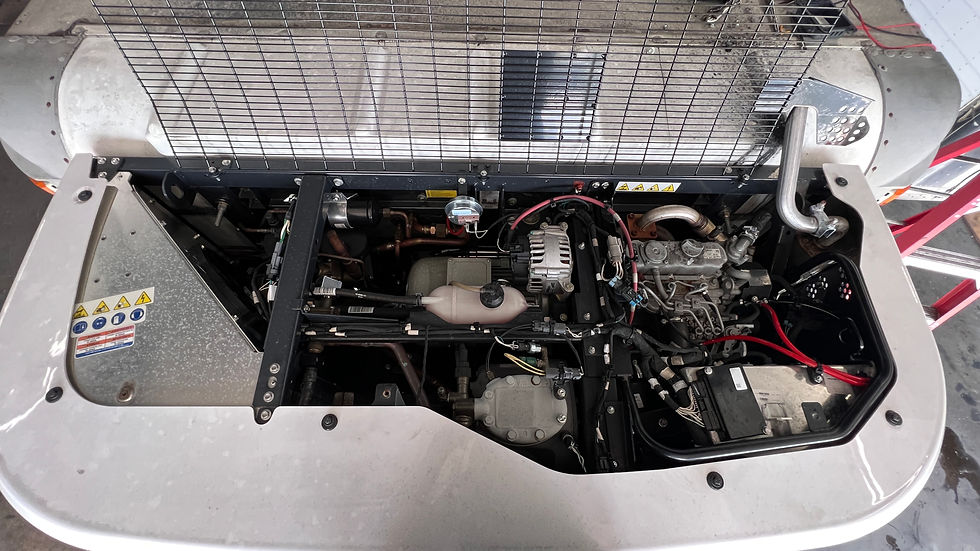
In this example, a Carrier self-powered truck unit features an engine, compressor, and optional shore-powered standby motor. Even though SPU may have the optional standby option, they still are capable of independent operation. Again, these units are completely self-reliant and require no assistance from the vehicle. Remember, all trailer-mounted units are by nature self-powered because they all are made to function independently of the vessel. Direct drive units on the other hand, only come in truck and vehicle-powered systems.

Direct Drive
Like their big brothers, the direct-drive units though smaller, perform the same job as the SPU. But because of their size and versatility, they've become a favorite of local food delivery and short-haul providers. The most significant difference between the two is mostly in their performance and capacity, though recent improvements have seen direct drive technology becoming a viable alternative to the larger self-powered unit. Still, any trade-off in capacity and performance with the direct drive is made up by their versatility. Direct drive units tend to be more user-friendly and convenient because they don't require special knowledge or licenses for drivers. This makes it much easier to find people to operate them.
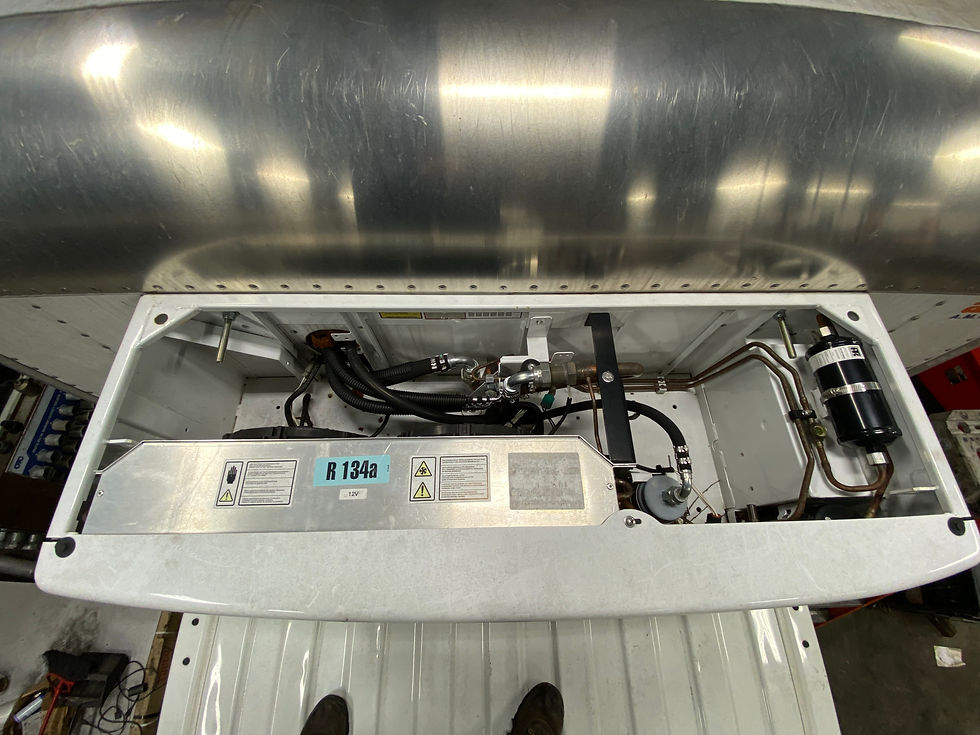
In this example, a Thermo King V-520, you can see that externally, the direct drive looks similar to the self-powered TRU with the large host unit sticking off the front of the box. But when you glance inside the unit, you'll notice that there is no engine or compressor, only some refrigeration plumbing, along with the condenser and fans. We might refer to these as "chillers" because many people only use them like mobile refrigerators; in such cases, the self-powered unit only needs to keep the product chilled.
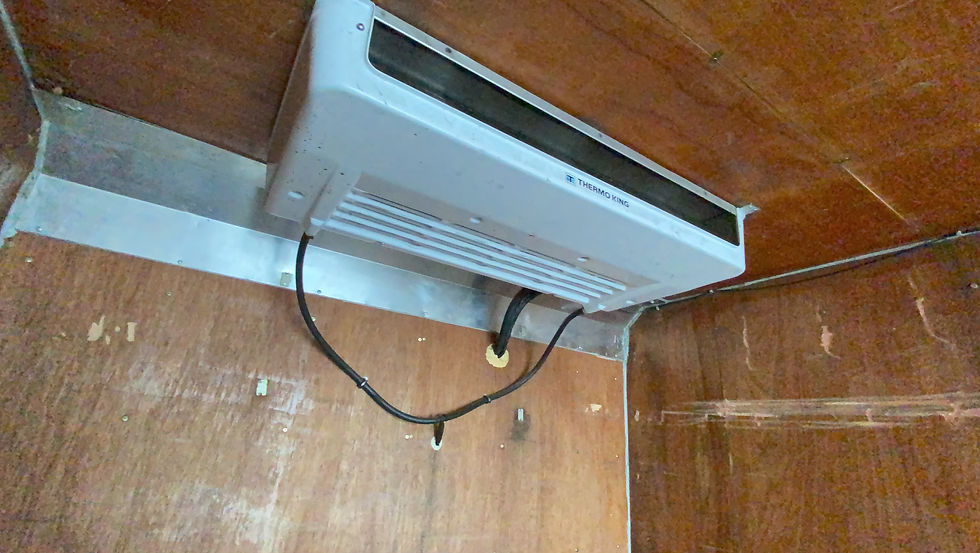
The rear of a direct drive features a stand-alone evaporator, with circulating fans; this is installed on the ceiling of the box and is connected to the host unit only by refrigeration lines, and communication and electrical power wiring.

The primary design difference is this automotive-style compressor that's "driven" by the vehicle engine crank. This makes these units extremely customizable and able to be retrofitted on many types of non-traditional refrigerated vehicles. This is probably what makes them a popular choice for suppliers who don't need the kind of heavy cooling capacity self-powered units offer. This also means that unless the truck engine is running, the unit is not performing any refrigerated operations. This is something to consider when choosing the right TRU application for an operation. This design difference could also be a limiting factor for many customers who need constant cooling operations regardless of unit performance or capacity. For example, Carrier's newest 50XR direct drive unit has nearly the same performance capacity as their self-powered Supra S-6, but only the S-6 can operate without the assistance of the truck. This means that if units need to be loaded in the middle of the night with fresh produce and ready to roll in the morning when the driver shows up, the Supra is likely the only option for this customer. Now one possible way this could work is to use a direct drive unit with an optional electric standby motor. However, if the customer doesn't have high-voltage horsepower hookups at their facility, this option isn't going to be possible and only the self-powered unit would be an option.
Technically Different, but Still the Same:
Of course, there are a lot of technical differences between self-powered units and direct drive units including size or configuration of components, logic and control systems, and performance, but what makes both of these units the same from a technician's perspective is their utilization of air-flow-driven refrigerant systems to perform cooling operations.
(NOTE: there are other types of refrigerated box systems, including cold plates and chiller box systems but in this series, we're only focusing on the primary TRU systems utilized in transport refrigeration here at Salem Leasing.)
What you need to know here is that the primary components across both self-powered and direct drive design platforms are the same. Both utilize the 4 primary components of the vapor refrigeration cycle and require the use of similar mechanical systems to circulate air to absorb and reject unwanted heat: Compressor, Condenser, Expansion Valve & Evaporator.

Performance Determines Utilization
Performance is the biggest factor when considering which one is best for a customer's operation. The overall cost of a direct drive system in combination with the type of vehicle it's being assigned to may be the less expensive option, but customers should always consider the requirements for protecting the product and choose an appropriate sized system. Manufacturers will generally use some kind of worksheet or formula to determine which unit might be best for a customer's application. This formula factors in several different performance and product requirements, along with the install vessel size and specifications. This sheet will allow the customer to determine what unit they should purchase.
Final thoughts:
Some might say that the direct drive is not a true TRU system because it requires an external power source to do the job. Again, they might also call the direct drive system a chiller because it usually only keeps temperatures in the chilled range, like a household refrigerator, but none of these things disqualify it from meeting the definition of a TRU. Remember, TRU stands for the transport refrigeration unit and the primary job of any TRU is to remove unwanted heat to maintain a safe climate-controlled space for the product during its journey through the supply chain. The direct drive unit is indeed, performing the duties of a transport refrigeration unit and therefore should always be considered as part of the TRU family.
In our next lesson, we'll dive a little deeper into some of the features of the TRU and begin to understand the design performance of the unit. This is important, not just for understanding how to work on or service them, but for creating the right kind of mindset for the customer and helping them manage expectations. We'll also begin to look at the different versions of Carrier and Thermo Kings truck and trailer units and get to know what makes them unique along with some of my own perspective on why each is made the way it is.
Comments